Laser micromachining, an established technology now in its fourth decade, has consistently excelled in high-precision material removal.
As industries increasingly demand greater precision, miniaturization, and cost reduction, along with the use of advanced materials, laser micromachining will continue to be a vital solution in the decades ahead.
MICROMACHINING PRECISION AND MATERIALS
Micromachining targets feature sizes between 1 micron and 1 millimeter, using various methods. Lasers excel particularly at the lower end of this range, especially with materials such as thin foil, glass, and polymers.
Their significant advantages include non-contact machining, ablation rather than melting, selective material removal, no line-of-sight restrictions, suitability for very soft or thin materials, rapid removal rates, and minimal to no need for post-processing.
Additionally, laser sources are highly adaptable and can be easily integrated with automation systems and software controllers, facilitating their incorporation into both new and existing production lines on the factory floor.
APPLICATIONS IN THE BIOMEDICAL INDUSTRY
Drilled micro-holes play a crucial role in various applications, serving to deliver or remove fluids and gases, block unwanted materials, provide access ports for devices, and act as selective barriers for certain materials.
In the biomedical field, these applications range from drug and device delivery to last-chance biologic filters, micropore or microwell array filters, cell counters, and microfluidic diagnostic tools.
The versatility required in hole sizes, shapes, aspect ratios, and densities to meet specific functional goals highlights laser micromachining as the primary enabling technology.
This preference is due to the advantages previously discussed, such as precision, non-contact processing, and the ability to work with delicate materials.
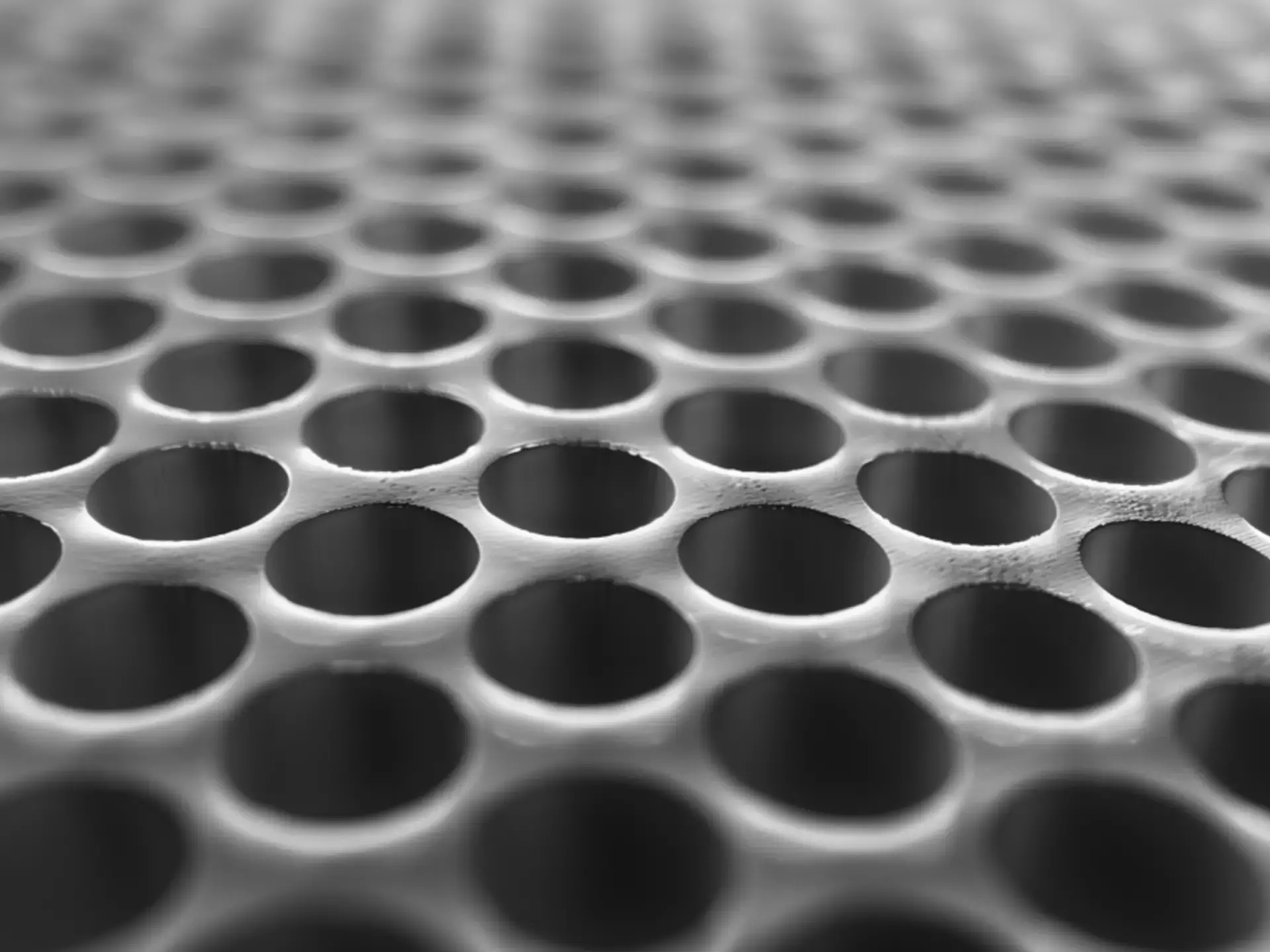
HIGH ASPECT RATIO AND HIGH-DENSITY DRILLING
CHALLENGES WITH POLYMERS AND THIN METALS
When it comes to working with polymers or very thin metals (including metal foils), many technologies struggle to achieve both efficiency and economies of scale in process times. This issue becomes particularly significant in biomedical applications where typical aspect ratios can reach as high as 50:1.
Given these demanding specifications, along with the varying material types and thicknesses, lasers often represent the only viable solution for both development and production phases.
For applications requiring very high density drilled holes, laser technology stands out because few other methods can achieve such high resolution. The theoretical resolution of a laser can approach twice the wavelength of the light source. By leveraging advanced optical design and a deep understanding of laser-material interactions, it is possible to achieve results very close to this theoretical limit.
In contrast, alternative methods often fall short when used with polymers, especially in the context of biomedical applications where biocompatibility and strict regulatory standards are paramount.
Lasers, therefore, not only meet the technical requirements but also adhere to essential health and safety regulations.
OPTICAL DESIGN AND ASSIST GAS UTILIZATION
The selection of a laser and the development of its process begin once the substrate material and its thickness are determined, and the desired feature size and pitch (with associated tolerances) are designed. The choice of laser primarily depends on wavelength, pulse width, and pulse energy.
Different materials have absorption spectra that dictate the optimal laser wavelength for machining. These wavelengths range across UV (<400 nm), visible (400-700 nm), and IR (>700 nm) spectrums. For instance, polymers are typically micromachined using UV or visible wavelengths, with polyimide showing strong absorption at 248 nm—a typical wavelength for KrF excimer lasers. Conversely, glass and metals are better suited to IR wavelengths, as glass shows significant absorption at wavelengths greater than 4000 nm, such as the 10600-nm output of CO2 lasers.
Higher laser pulse energies are generally preferable as they enable faster material removal and can achieve greater depths. As machining progresses deeper into the substrate, higher pulse energy helps overcome beam shielding caused by the sidewalls of the drilled hole. Additionally, higher pulse energies extend the laser's operating life and enhance throughput, allowing for beam splitting to simultaneously process multiple parts. However, the trade-off with higher energy delivery can include negative effects like melting, charring, or poor edge control on the substrate.
Laser pulse width—measured in nanoseconds, picoseconds, or femtoseconds—indicates the duration over which the pulse's energy is delivered. A shorter pulse width at the same energy level delivers higher power, favoring material ablation over melting. In recent years, ultrafast lasers with pico- or femtosecond pulse widths have greatly enhanced our capability to drill faster, deeper, and with higher quality holes without the need for post-processing. Nevertheless, these advantages sometimes come at the cost of reduced throughput and higher initial costs for the laser equipment.
Once the appropriate laser source is determined, optical design plays a critical role in delivering the raw beam from the laser to the substrate. Optical design engineers use mirrors and lenses to create a beam path that aligns and manipulates the beam, achieving a focused spot size for direct writing or a projection for systems like excimer lasers using masks. Most direct write systems utilize either a fixed or a scanned beam to drill holes. Scanning is often done by a galvo scanner, which can operate on single, dual, or multiple axes for precise and rapid beam movement. In mask projection systems, a specially designed and fabricated mask allows for simultaneous drilling of multiple holes at the desired size and pitch.
The use of assist gases is also crucial in applications involving high aspect ratio and high-density hole drilling. Assist gases can improve throughput, cool the substrate, prevent the redeposition of debris, and inhibit the formation of ablation byproducts through shielding. Common choices for assist gases include oxygen (O2), nitrogen (N2), argon (Ar), and neon (Ne), with the gas delivery system being meticulously designed to be always on, coaxial with the beam, or off-axis depending on the application's specific requirements.
MANAGING SUBSTRATE MATERIAL AND PROCESS ADAPTATIONS
Managing the substrate material during laser micromachining is paramount due to potential movements, shifts, or deformations as stresses are relieved and material strength decreases, particularly noticeable in high-density drilling. Engineered fixtures are used to hold the substrate in place. Alternately, staggered machining strategies move the laser beam to different areas to allow the material time to relax or cool after drilling.
Moreover, the tolerances of raw materials, especially polymers, are generally wider than those of the laser beam and associated optics, sometimes by orders of magnitude relative to the laser wavelength. Advanced closed-loop feedback systems employing high-resolution cameras, plume detectors, vision systems, and software are integral for detecting and compensating for any changes during the process, ensuring uniform quality and dimensions. This might involve adjusting the number of laser pulses directed at a specific hole or area. Such laser micromachining systems equipped with closed-loop feedback exemplify a significant advancement in materials processing, showcasing the laser's capability to rapidly and accurately adjust parameters to deliver consistent, high-quality results.
THE IMPACT ON BIOMEDICAL TECHNOLOGIES AND QUALITY OF LIFE
As societal awareness and appreciation for a better quality of life grow, there is an increasing demand for more disease-free time and shorter treatment and recovery periods. This shift is driving biomedical technology, including diagnostics, towards smaller, more precise solutions that utilize novel materials designed to meet these needs in a growing population.
As the development of new processes and designs focuses on efficiency, accuracy, and cost reduction, laser micromachining continues to evolve in tandem, maintaining its role as a critical enabling technology. This evolution ensures that advancements in health care and medical device technology can keep pace with the expectations and demands of modern society.