Fiber end caps from OpTek deliver optimum performance, created by fusion splicing or laser fusing short lengths of material to the fiber end face.
Fiber end caps are required for a number of applications including the creation of collimators, to allow expansion of high power fiber laser beams to reduce the power density at the air/silica interface and to protect structured fibers against environmental ingress. Laser processing allows the large core fibers to be cleaved, free of the hackle and chips observed with mechanical scribing techniques, prior to the splicing operation. Following the splicing operation, the end caps can be laser cleaved to the final protrusion (length), angle, and orientation (i.e. stress rods) specifications. End capping may also be applied in combination with laser lensing to create an all silica construction with the optimum optical characteristics.
End capping requires splicing or fusing “coreless” fiber to single-mode (SM) fiber or multimode (MM) fiber transmitting/gain fiber in an attempt to reduce power densities (J/cm2), thus increasing the damage threshold of the component. The end capping process is often challenged by the ability to cleave large fibers (200-600µm), splice the fibers to the end cap, and precisely cleave the end cap relative to the splice point. Cleave angles to control back reflections are often necessary and PM fibers require the stress rods to be positioned relative to the cleave angle.
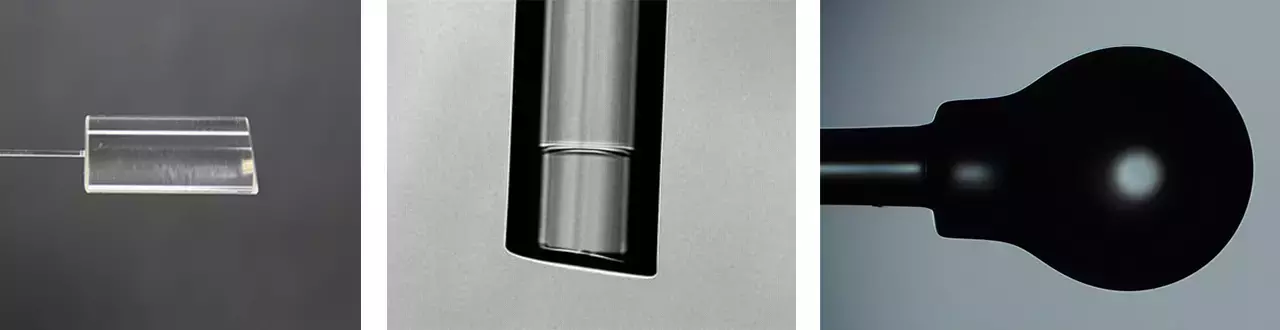
Additionally, properly designed end caps can alter the numerical aperture (NA), mode field diameter (MFD), and beam direction and properties (FL, Waist, etc.) from the transmitting fiber. The end caps can also minimize undesirable Fresnel reflections from the fiber end face.
In applications requiring a greater expansion of the beam at the air interface than can be achieved within the diameter of the fiber, laser fusing is used to join end caps with a significantly larger diameter. By controlled delivery and profiling of the laser energy, a strong and reliable join is achieved regardless of the size mismatch. OpTek’s proprietary LaserCleave™ process delivers controlled end face geometry and angle control while sealing the open structure of structure optical fiber against the ingress of environmental elements.
Applications include:
• High power fiber laser
• Collimators
• Sealing PCF
End capping for high power devices
End capping requires splicing or fusing “coreless” fiber to single-mode (SM) fiber or mutimode (MM) fiber transmitting/gain fiber in an attempt to reduce power densities (J/cm2), thus increasing the damage threshold of the component. Additionally, properly designed end caps can alter the numerical aperture (NA), mode field diameter (MFD) and beam direction and properties (FL, Waist, etc.) from the transmitting fiber. The end caps can also minimize undesirable Fresnel reflections from the fiber end face. The end capping process is often challenged by the ability to cleave large fibers (200-600μm), splice the fibers to the end cap, and precisely cleave the end cap relative to the splice point. Cleave angles to control back reflections are often necessary and PM fibers require the stress rods to be positioned relative to the cleave angle. | ![]() |
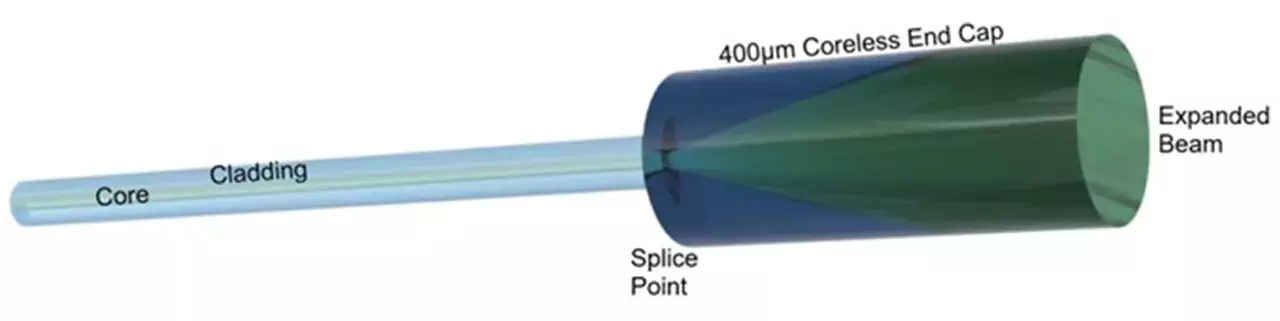
Laser processing allows the large core fibers to be cleaved, free of the hackle and chips observed with mechanical scribing techniques, prior to the splicing operation. Following the splicing operation, the end caps can be laser cleaved to the final protrusion (length), angle, and orientation (i.e. stress rods) specifications. This laser cleaving operation also accommodates high-power applications that would otherwise heat-up from heavy absorption from embedded polishing compounds.
End Caps: | Turnkey End Cap Assembly: | ||
125μm Coreless 250μm Long | ![]() | Coreless fiber | ![]() |
250μm Coreless 1.0mm Long | ![]() | Kovar Housing | ![]() |
2.0mm Coreless 3.0mm Long | ![]() | Hermetically sealed (solder or glass frit) | |
200μm Coreless Lensed | ![]() | AR Coated |
Laser processing also accommodates multi-segment/multi-fiber constructions:
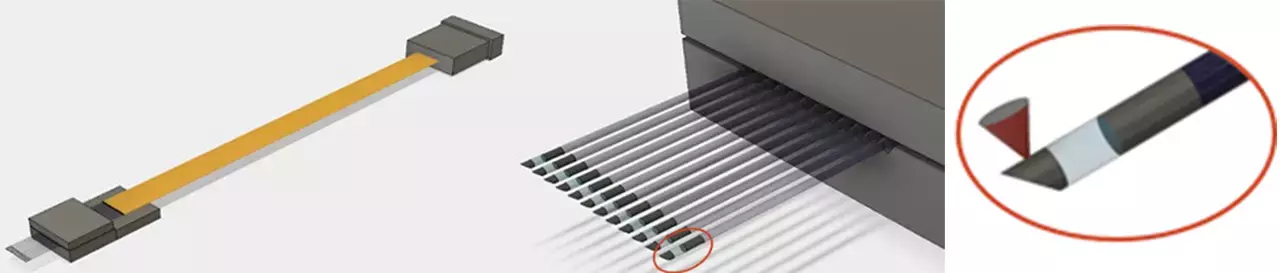
Collimators:
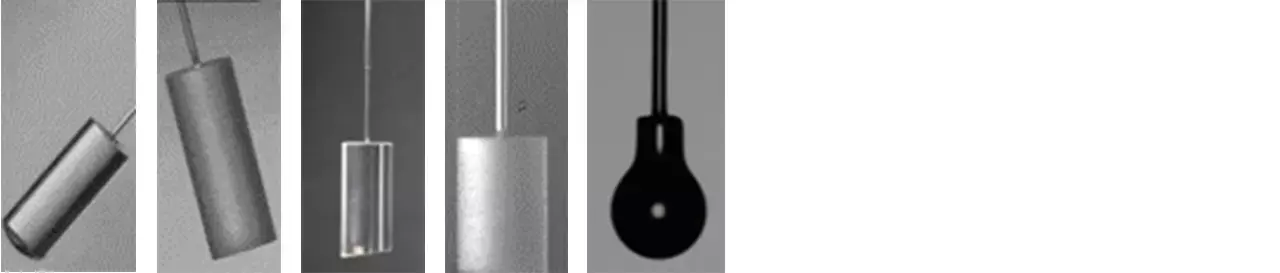