OpTek laser lensing produces high-performance lens forms directly onto the end of an optical fiber.
The non-contact lensing process is an incredibly fast alternative to mechanical polishing and uses on-line imaging to ensure accurate centration of the lens to the fiber. The optical quality of the laser created lens is unsurpassed. The reproducibility of the lens and the exceptionally low-scatter of the processed surface provides enhanced performance in any active coupling application.
Lensed fibers are often the method of choice for interfacing optical fiber to active devices and waveguides. Lensing technology provides highly efficient coupling with precise radii control (± 1.0µm) and in-situ beam monitoring (far field ratio) while consuming a fraction of the space and costs of bulk optic alternatives. Fiber lenses are typically created to match the emission profiles of the receiving or transmitting device to which they are coupled.
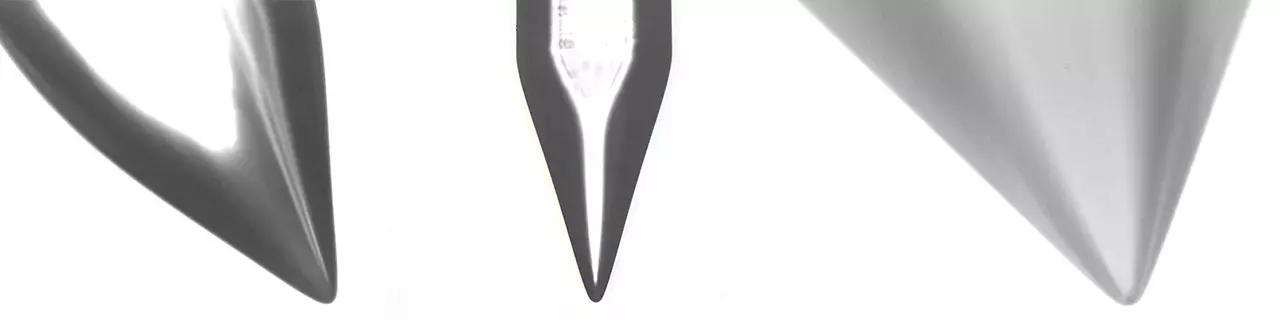
In high power applications, the LaserCleave™ process gives very high damage-threshold surfaces, which can also be produced directly on free-standing fibers, and if necessary, on non-round fibers. The laser lensing process also offers PM stress rod alignment control, making it suitable for a variety of applications, such as Fiber Optic Gyroscopes (FOGs), pump lasers, waveguides, and a number of sensing applications. In all cases, the speed of OpTek’s laser lensing process makes it the most cost effective method for lensing optical fiber.
Moreover, the reliability and reproducibility of the lensing process, together with the ability to process parts already assembled into fixtures or ferrules, allows the whole manufacturing sequence to be optimized, with the laser cleaving process, which produces the final optical quality end, carried out as the final step in the assembly.
LASER LENS ADVANTAGES:
Lens Radius
• <3-20µm for standard process
• Typical tolerance is ±10%
Lens Orientation
• Lens orientation to polarization stress rods (+/- 3 degrees)
• Orientation to ferrule
Speed
• 10’s of seconds per lens (depends on type)
Precise Lens Position
• Lens position can be referenced to fixed feature on the fiber such as metallization
High Damage Threshold
• Laser lensing produces high damage-threshold facets for use in fiber-laser applications
Geometric Form
• Choice of precise shape of end-face, including angled lens forms and removal of scrap angles
• Lens forms include conical, wedge, bionic, and ball lenses
Optical Quality
• Lower scatter than conventionally polished ends
Non-Contact Process
• No tool wear, or mechanical damage to the fiber
Increased coupling efficiency, decreased alignment sensitivity
• Matching far-fields between fiber lens and active device leads to improved coupling efficiency
• Decreased alignment sensitivity leads to quicker lock-down, lower manufacturing costs
Centration
• Active centration around the actual core means proper lens positioning