Many of our customers use laser scribing & dicing processes because it is damage free with minimum heat affected zone and high speed. Applications include: EV components, sensor manufacturing, semiconductor & PV manufacturing and biomedical materials
Laser scribing and dicing is used to produce features from a few microns to many meters in materials that are hard to machine by conventional methods in challenging materials like diamond, organics, silicon or very delicate, multi-layer polymer films. Our global collection of world leading facilities featuring state of the art ultra short pulse laser technology, machine vision and precision motion.
We help customers with highly complex and intricate profiles in flat, curved, and complex shaped parts. This includes scribing profiles on wires and optical fibers, processing tubes, and cylinders, along with flat sheets and material fed from a roll or spool. Multi-layer materials can also be laser cut without the loss of definition or delamination of the individual layers, even with very thin or delicate materials.
With decades of delivering high quality processes parts to our world wide customer base, OpTek can address your precision cutting requirements from prototype level through to full-scale production.
Materials that can be processed by laser cutting include:
METALS | POLYMERS | PLASTICS | OTHER |
---|---|---|---|
Alloys | Polyimide | Zirconia | Diamond |
Steels | Polyethylene | Green Ceramics | Sapphire |
Copper | PMMA | PZT (Lead zirconate titanate) | Quartz |
Aluminium | Kapton | Silicon nitride | Glass |
Tungsten | Vespel | Ceramic | |
Titanium | Cirlex | ||
ABS |
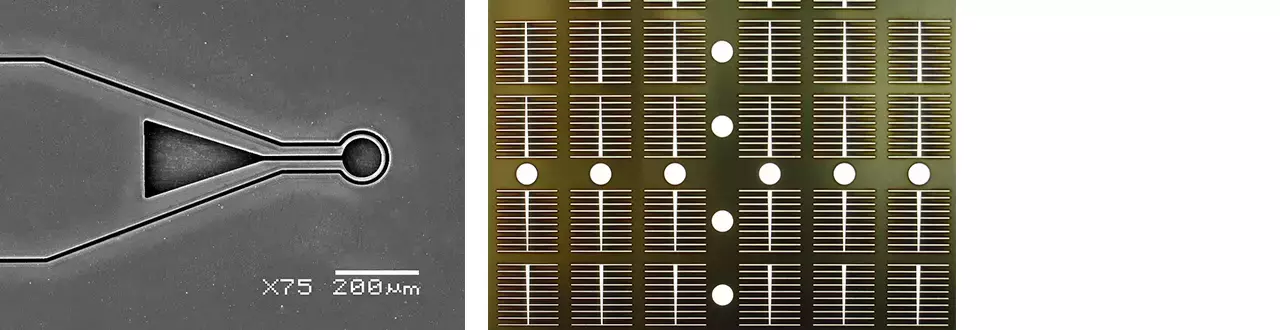
Full-thickness (through) cutting provides the flexibility to create curves, circles, and other non-straight profiles, in addition to the more conventional straight-line cuts. Through cutting also makes it possible to dice out sections, or devices from the centre of a wafer, without damage to the surrounding material. Partial-thickness laser dicing provides fast, accurate, and reproducible processing of a substrate, which can then be reliably cleaved or snapped into individual die. This scribe and snap approach delivers the advantages of high speed, narrow kerf processing, with minimized machining debris and low thermal impact.