In the dynamic realm of medical device manufacturing, precision and quality are paramount. As technology advances and the demand for smaller, more intricate medical devices grows, traditional methods of stripping insulation from wires, optical fibers and cables can prove cumbersome and imprecise.
The inception of laser wire stripping can be traced back to a 1976 NASA research program aimed at improving wire-stripping methods. The research program showed that the conductor reflected laser energy, leaving it undamaged, whilst reliably stripping the insulation material away.
After the introduction of the first commercial CO2 laser wire stripping machine, there arose a growing demand for further advancements in laser technology. This demand was fuelled by the need to accommodate a wider array of insulating materials and wire types.
The catalysts for this need included the emergence of novel insulation varieties, innovative methods of applying insulating material to wire, varying bonding characteristics, and a shift toward smaller, lighter wire applications. Concurrently, new products utilizing these wires were also being developed across aerospace, defence, medical and consumer electronic applications.
Conventional wire stripping techniques had evolved to encompass mechanical, abrasive, chemical, and thermal methods. Nevertheless, each of these methods carried its own set of associated issues, ranging from conductor damage and sluggish processing speeds to imprecise results and subpar quality.
In this article, we will delve into the significance of laser stripping for non-fiber medical devices and how OpTek Systems is pioneering this transformative process.
The benefits of laser stripping & ablation
The utilization of lasers for the full or partial removal of insulation or coating layers from electrical wires, catheters, and various medical devices has become a standard practice, owing to the multitude of advantages it offers. Lasers can remove such coating layers from single or multifilar wires and single or multilumen catheters. The high resolution of the laser light (theoretically its wavelength) can focus on individual wire strands or lumens to enable specific functionality of the device.
Firstly, laser stripping provides consistently high-quality results owing to its inherent nature. When employing a suitable laser for stripping polymer insulation from a wire conductor, the laser energy is efficiently absorbed by the insulation while being highly reflected by the underlying metal conductor. This reflective property of the conductor eliminates any risk of damage during the stripping process. Regardless of the wire's size, laser stripping can be applied without jeopardizing the integrity of the conductor.
Furthermore, laser stripping machines exhibit remarkable versatility, capable of handling wires and cables in various shapes, including round, out-of-round, and flat ribbon. This is primarily due to the fact that it's a non-contact process and the laser beam can be meticulously controlled, allowing for the creation of a wide array of stripping patterns, some of which are nearly impossible to achieve through other methods.
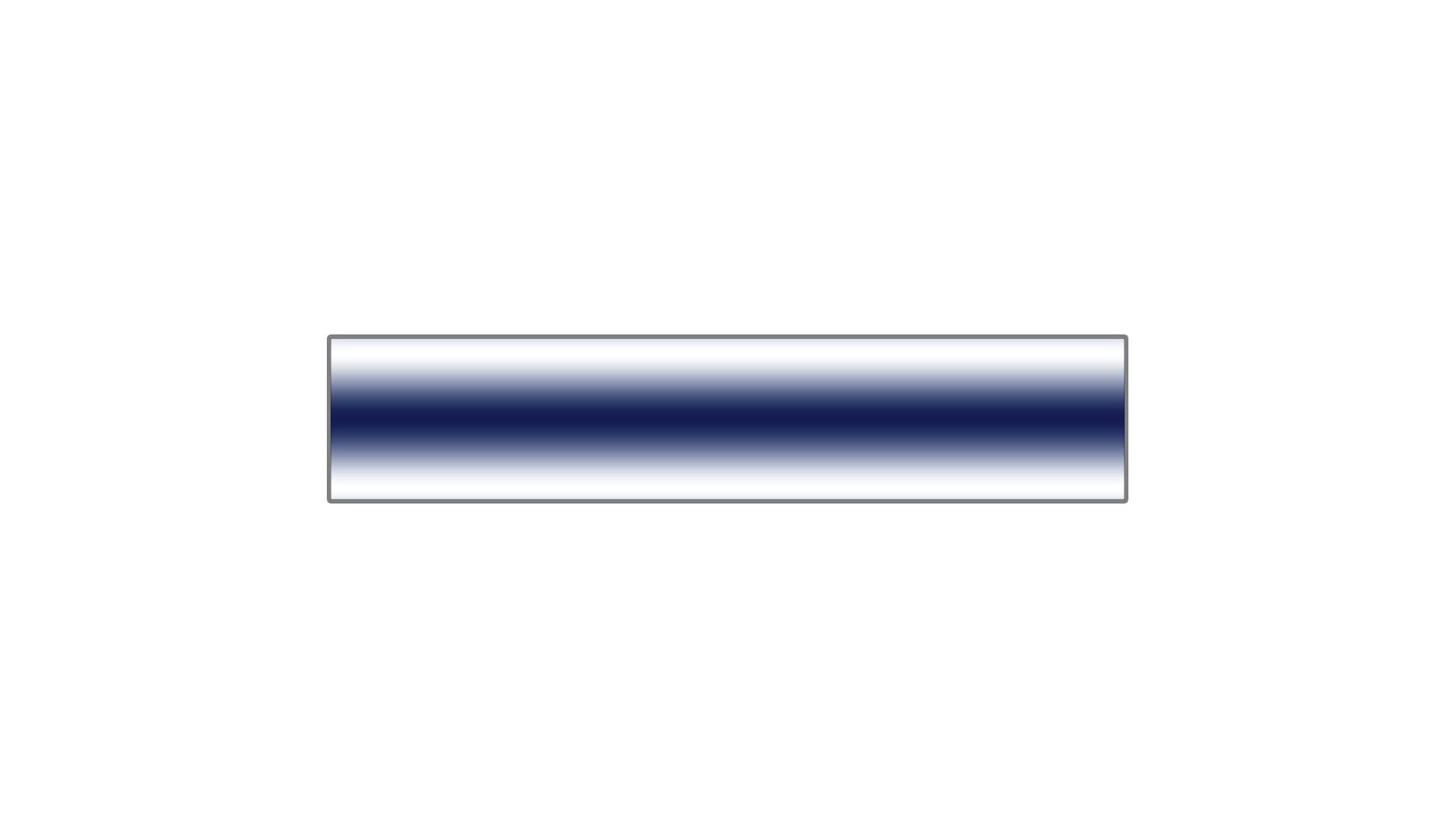
OpTek's innovative laser stripping processes include
This involves crosscutting or crosscutting and slitting to precisely remove insulation or coatings from the wire or cable ends.
It is possible to thin or remove different layers of insulation from the substrate material, this can be done with multiple laser sources for optimum performance and speed.
Laser wire stripping can create windows in the insulation or coating, leaving specific sections exposed while protecting others.
For even finer control, a mini window can be created, offering an even smaller exposed area within the insulation.
Laser wire stripping can achieve angled cuts, enabling unique stripping geometries tailored to specific needs.
Laser technology allows for the programming of stripping patterns at any point along the wire or ribbon cable, providing unparalleled flexibility and customization.
This exceptional ability to direct the laser beam for various stripping patterns not only enhances precision but also opens up new possibilities that would be challenging or even impossible to achieve with alternative methods.
Another notable advantage lies in the user-friendliness of the laser stripping process. Unlike mechanical stripping methods, there are no blades to replace or consumables to replenish, simplifying maintenance and operation. Additionally, it is a non-contact process, eliminating components that wear out and reducing maintenance requirements.
Laser stripping machines come in a variety of types, each with different wavelengths, enabling users to select a laser that readily absorbs the layer to be removed while strongly reflecting from the underlying material.
Moreover, laser strippers can be seamlessly integrated into both semi-automatic and fully automated processes. In semi-automatic setups, operators merely present the material to the machine, ideal for end stripping, whether for single ends or batch processing. Full integration with downstream cut-and-strip machines allows for automated measuring, cutting, and stripping.
Furthermore, laser stripping ensures no damage to the metal conductor, even if it's plated with metals like tin or silver. This reduces the need for extensive quality assurance measures and allows for tighter tolerances and lighter-weight wires.
Advantages also include the ability to process nearly all insulation types, versatility in handling various wire sizes and forms, precise tolerances of +/- 25 µm (0.001 inch) for precision applications, and the capability to program variable strip patterns to remove insulation at any desired location on the wire. These benefits collectively contribute to reproducible results, increased productivity, and cost reduction.
Compatible with various cable and wire insulation types
Laser wire stripping has the capacity to handle various types and configurations of wire and cable insulation.
- Single-core wires
- Twin leads
- Twisted pairs
- Multi-conductor cables
- Shielded or screened wires and cables
- Ribbon cables
- Coaxial cables
- Complex 2D and 3D shaped conductors, such as coils
- Variable Cable Sizes
- Wire gauges ranging from 1 AWG to 50 AWG or smaller
- Ribbon and flat cables with widths up to 285 mm (11.4 inches)
- Tubes
- Single and multi-lumen devices
- Polyimide
- PEB
- PTFE / Teflon®
- Silicone
- PVC
- Kapton®
- Mylar®
- Kynar®
- Fiberglass
- ML
- Nylon
- Polyurethane
- Formvar®
- Polyester
- Polyesterimide
- Epoxy
- Enameled coatings
- DVDF
- ETFE / Tefzel®
- Milene
- Polyethylene
- PVDF and other materials, whether they are hard, soft, or designed for high-temperature applications
Laser stripping for medical applications
In the realm of medical device manufacturing, the meticulous selection of wires and cables, along with their precise processing, holds immense significance. Sometimes, this choice can even mean the distinction between life and death. Laser wire stripping emerges as a dependable method to ensure superior processing quality across a spectrum of medical applications.
Catheters serve as vital tools for guiding medical probes or devices within the human body, demanding utmost precision in wire size reduction to enhance manoeuvrability and functionality.
Common applications encompass Radiofrequency (RF) ablation, where catheters bear numerous conductors, including thermocouples and RF ablation signals. The fine wiring in these cases is often coated with materials like enamel (e.g., polyimide) or biocompatible fluoropolymers. Traditional mechanical stripping methods can inadvertently damage these ultra-miniature wires, but laser wire stripping guarantees a flawless, nick-free strip as the laser reflects off the conductors.
Pacemaker electrodes, with their flexible, spring-like structure and fluoropolymer coatings, present specific challenges for laser ablation due to heat sensitivity during processing. Nevertheless, these challenges can be readily overcome with careful laser selection and precise processing techniques, rendering laser stripping a viable and attractive option.
Medical power tools, such as those employed in brain surgery, demand unparalleled quality and reliability. Conventional mechanical brushing and abrading methods used on enamelled motor windings can introduce hazardous particulates into the final product. In contrast, laser stripping offers a clean, risk-free alternative.
Hypotubes, extended metal tubes with micro-engineered features along their length, serve as crucial components in minimally invasive catheters used alongside balloons and stents to clear clogged arteries. During the manufacturing process, it becomes necessary to remove portions of the extruded coating (e.g., PTFE, ETFE, or nylon-based compounds). Laser removal has gained popularity as an alternative to traditional blade-based methods, primarily due to its automation potential, which saves time, reduces costs, and minimizes errors.
Small-gauge single conductors are prevalent in a variety of medical devices, from catheter-delivered devices to cochlear implants and hearing aids. Leveraging laser stripping technology allows wires as tiny as 50AWG and smaller to be stripped without damaging the conductor.
Flat micro-coaxial ribbon cables are essential in numerous medical device interconnections, such as ultrasound machines. These applications necessitate the transmission of high-density, high-frequency signals through the most flexible cabling possible, requiring the use of ultra-small conductor sizes in high-density micro-coaxial ribbons. Due to the minuscule wire size and demanding precision levels, laser stripping emerges as an ideal solution, guaranteeing top-notch results in ultra-small, critical application cables.
OpTek Systems: Pioneering Laser Stripping Technology
OpTek Systems stands at the forefront of laser stripping technology for non-fiber medical devices. With a commitment to delivering excellence in precision and quality, they have developed cutting-edge solutions tailored to the unique requirements of the medical device industry.
OpTek Systems employs state-of-the-art laser systems that are designed for intricate, high-volume medical device manufacturing. These lasers are capable of stripping various types of insulating materials, including polymers, Teflon, and even Parylene, while maintaining the integrity of the underlying wires.
Why choose OpTek Systems for your laser stripping needs
Pathway to full production
OpTek Systems provides you the tools, support and expertise needed to take your project from R&D to over 1,000,000 units produced annually. Our team of experts are well positioned to assist you regardless of the size and scale of your project.
Customized Solutions
Recognizing that each medical device has its own set of specifications, OpTek Systems provides customized laser stripping solutions. Our team of experts collaborates closely with clients to design and implement laser stripping processes that precisely match the device's requirements.
Cost-Efficiency
Laser stripping not only improves precision but also reduces material waste and labour costs compared to traditional methods. OpTek Systems' solutions enhance efficiency in manufacturing processes, resulting in cost savings that can be passed on to customers.
Quality Assurance
OpTek Systems places a strong emphasis on quality assurance. Their laser stripping technology ensures consistent and reliable insulation removal, contributing to the overall safety and performance of medical devices.
Conclusion
In the ever-evolving landscape of medical device manufacturing, precision and quality are non-negotiable. OpTek Systems has emerged as a leader in this field by harnessing the power of laser stripping technology. Our commitment to innovation, customization, cost-efficiency and quality assurance positions us as a trusted partner for companies seeking to elevate their medical device manufacturing processes.
As the demand for smaller and more intricate medical devices continues to rise, laser stripping by OpTek Systems is poised to play a pivotal role in ensuring that these devices meet the highest standards of performance and safety. The future of medical device manufacturing is here, and it's laser-focused on precision and excellence, thanks to OpTek Systems.